Two years in the making, this summer, we embark on the biggest project the house has seen this century, restoring the mansard roof.
Introduction
When we first set eyes on the house in 2019, we knew the roof would need some work. The extant of work would take time to unravel. In this post, we will review the history and details that make up this victorian mansard roof, along with covering the scope of work and timeline.
Here are a collection of photos showing the roof over the years.
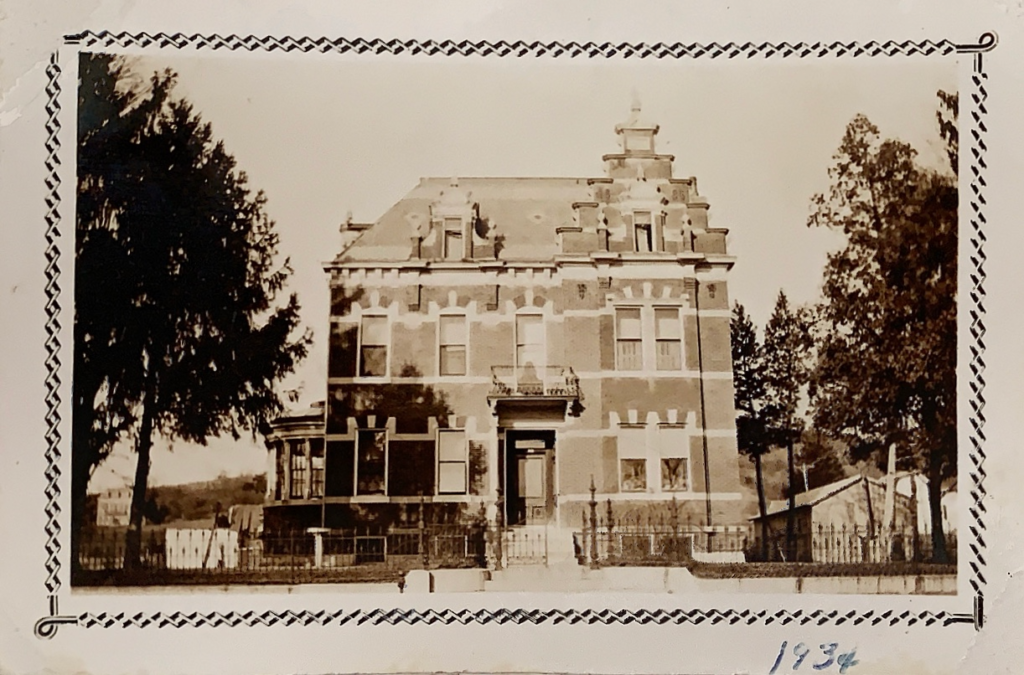
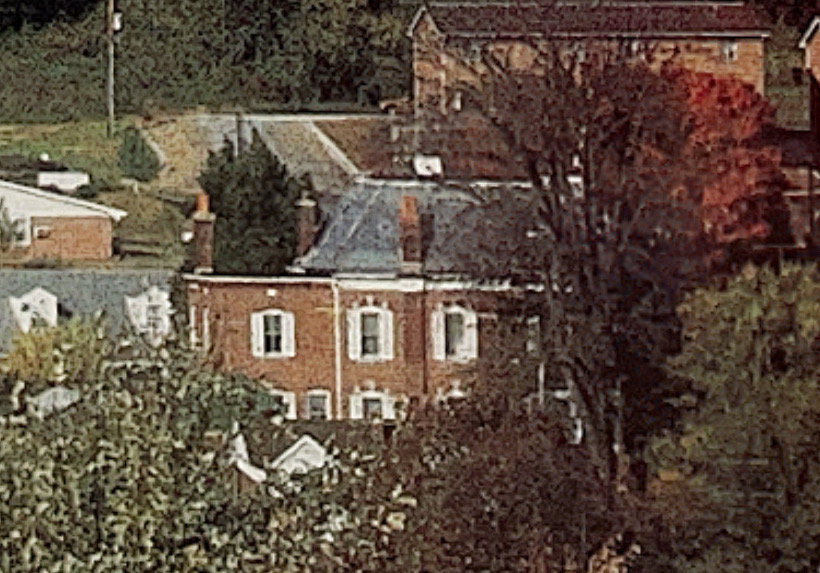
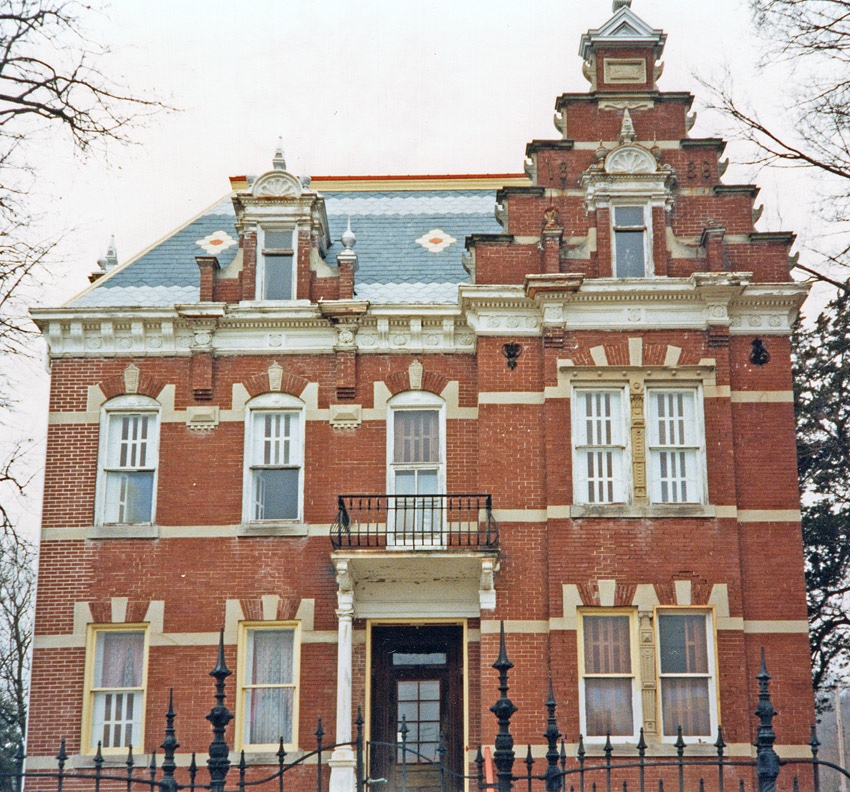
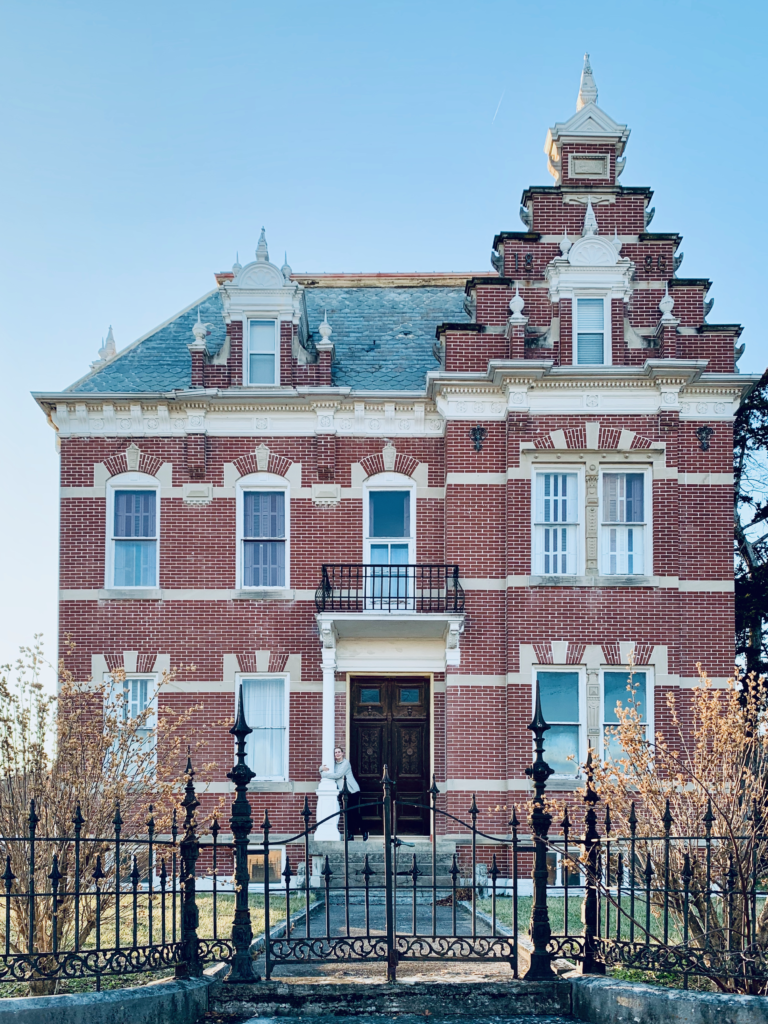
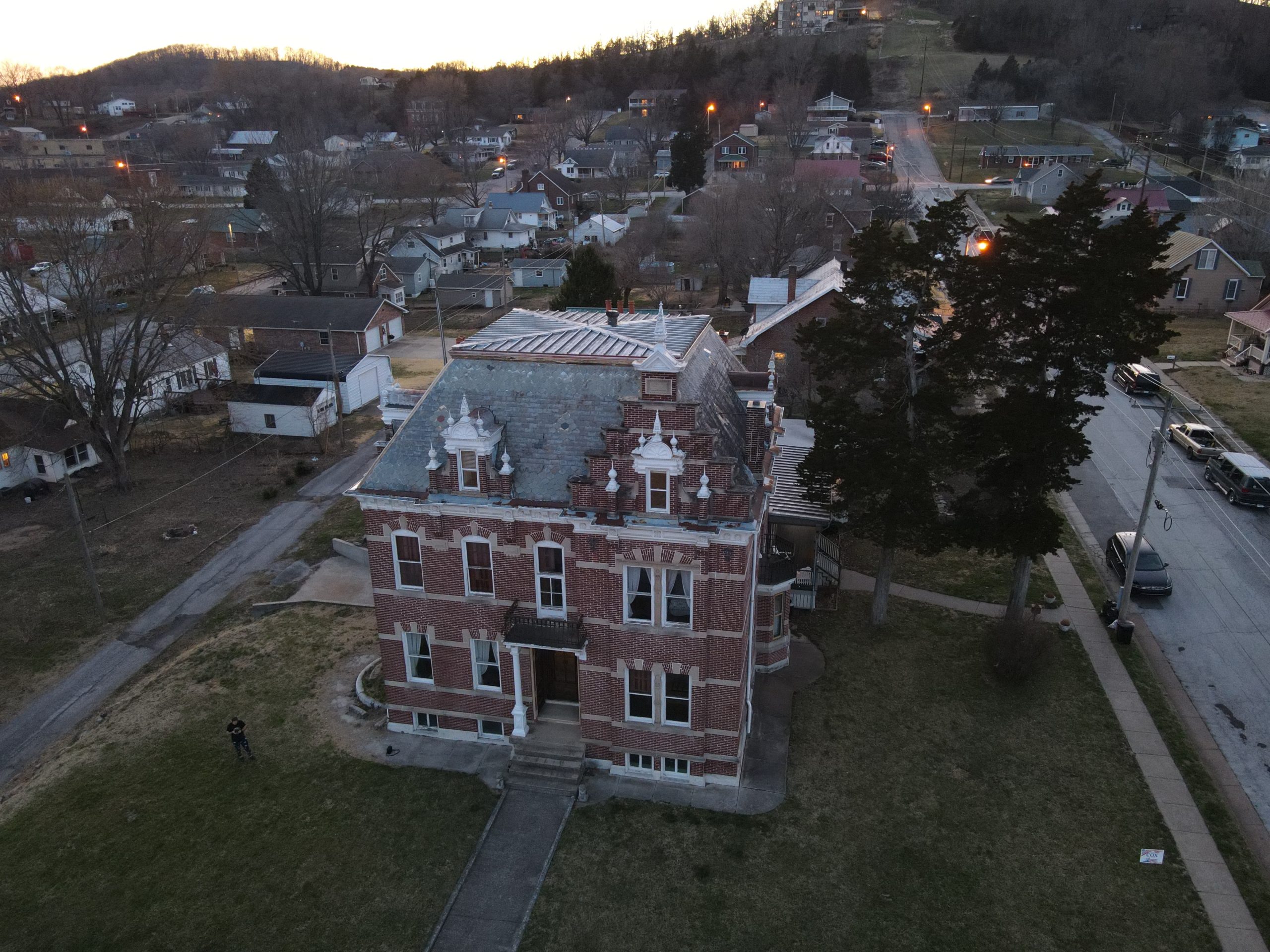
Slate Mansard
We have spent the past two years working with consultants and contractors and researching the best path ahead for the mansard roof.
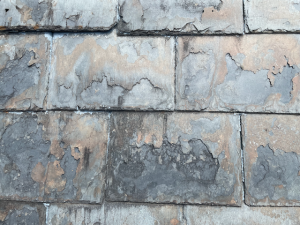
The Problem
The current slate roof faces three major issues:
- The slate was painted in the 1990s, and as a result, many tiles are beginning to delaminate.
- Most of the slate is Pennsylvania black, with a life span of about 100 years.
- A major valley flashing is beginning to fail, resulting in a leak that was “fixed” only to be undone by the expansion/contraction during the winter.
We hired a consultant in 2020 to assess the slate. Even though the slate had been painted, we were given a life expectancy of around 20 years. The primary issue is the combination of the delaminating slate and the failing flashing. Exploring the cost of fixing a major valley became the motivator for looking at the whole mansard roof.
The Solution
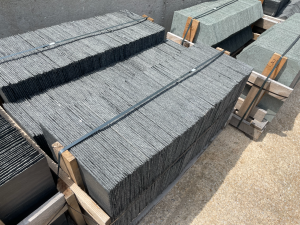
We are replacing the slate with Vermont S1 grade slate, which has a life span of up to 200 years. We are closely matching the same “floral” pattern with a combination of black, green, and red slate tiles. All flashing is being replaced with 20-ounce copper, and the original inlaid gutters are being brought back to life.
Sorry, honey, your dream kitchen will need to wait.
– A brave husband named Michael
While the slate makes up most of what you see on the mansard roof, there is a lot of water management from restoring the built-in gutters, copper flashing, and dormers.
Architectural Built-in Gutters
Restoring the original built-in gutters is nearly equal in scope and complexity to replacing the slate. In the 1990s, the original built-in gutters were covered with galvanized steel, and aluminum k-style gutters were hung. We are going back to the original built-in gutters with 20-ounce copper.
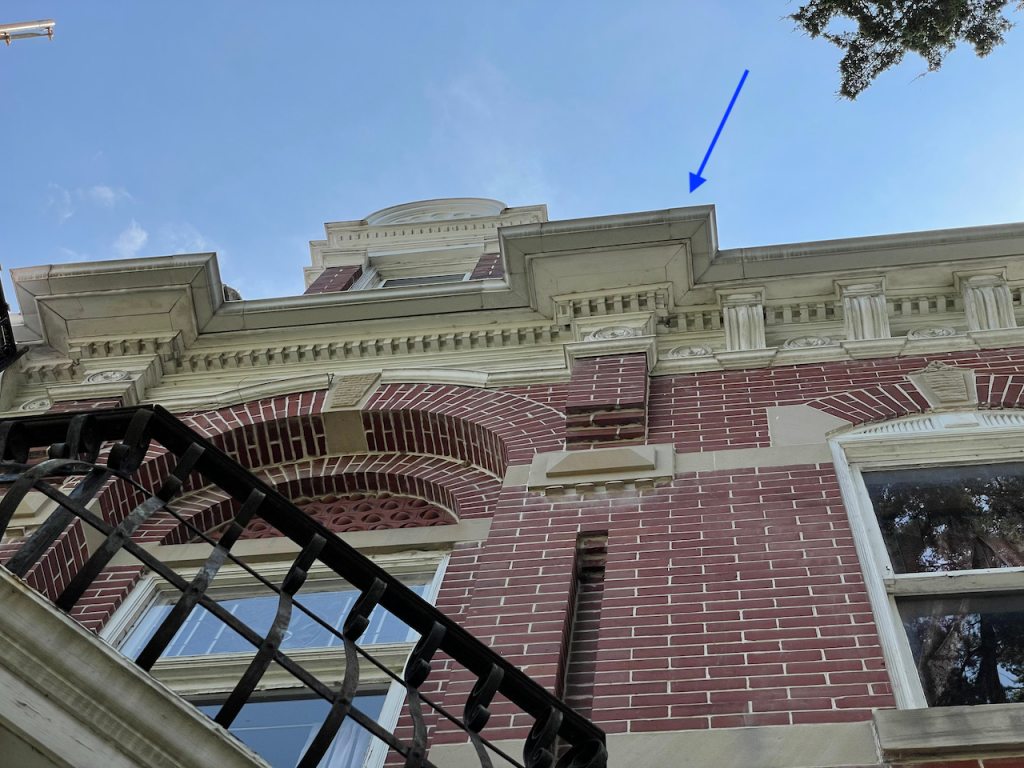
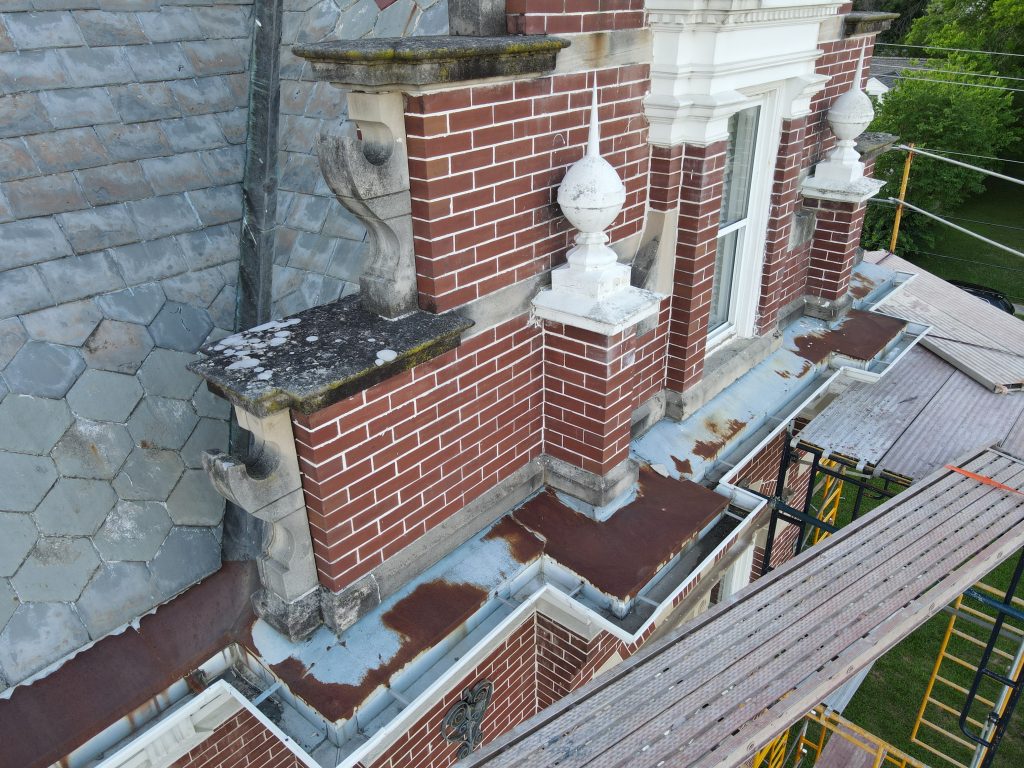
Dormers
Most of the metal work on the house is terne-coated steel. Three barrel dormers need restoration. Terne-coated steel requires painting and can show signs of rust in as little as a year1. To preserve the architectural detail, the rust will be cleaned up, and a special coating applied.
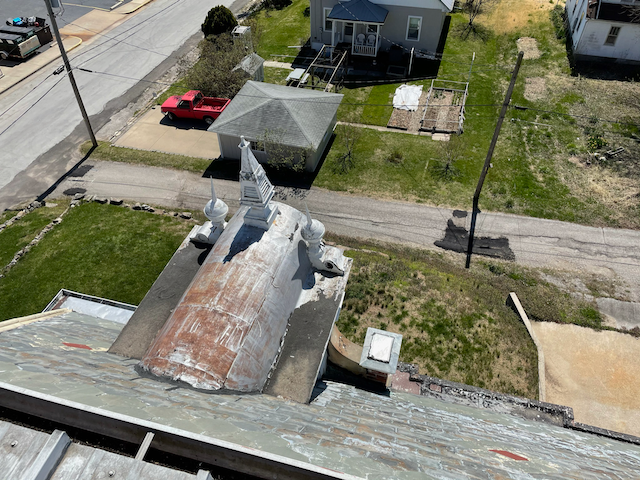
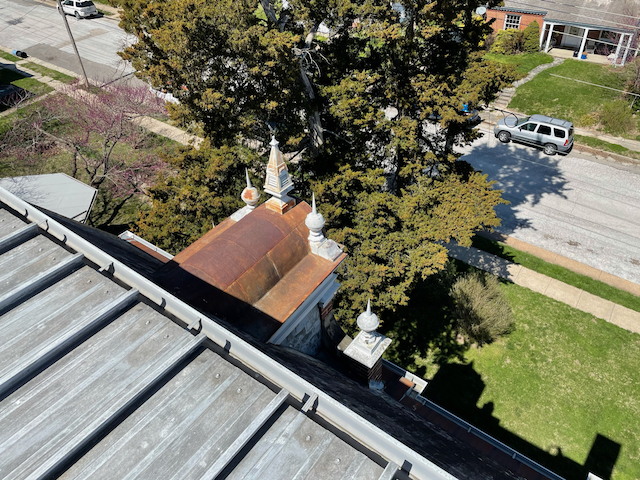
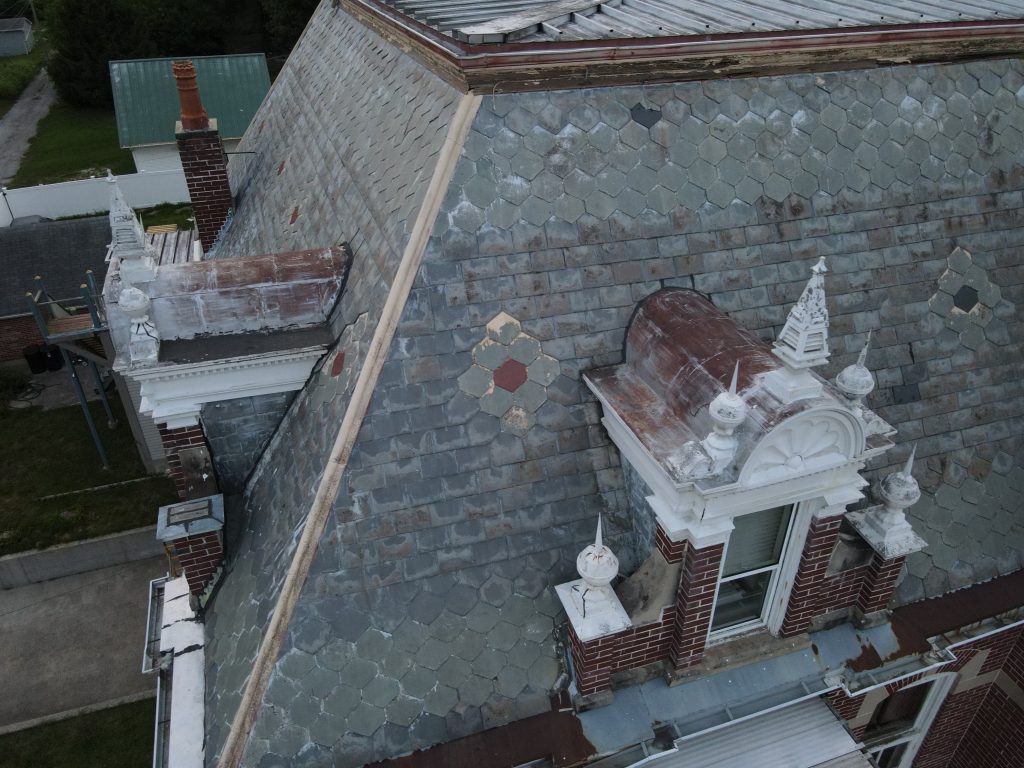
Crown
The upper crown has seen better days. One of the first items is extracting a sample of the crown and sending it to our millwork company in St. Louis for reproduction. We are working with the same millwork company that has reproduced the interior casing seen in the library restoration.

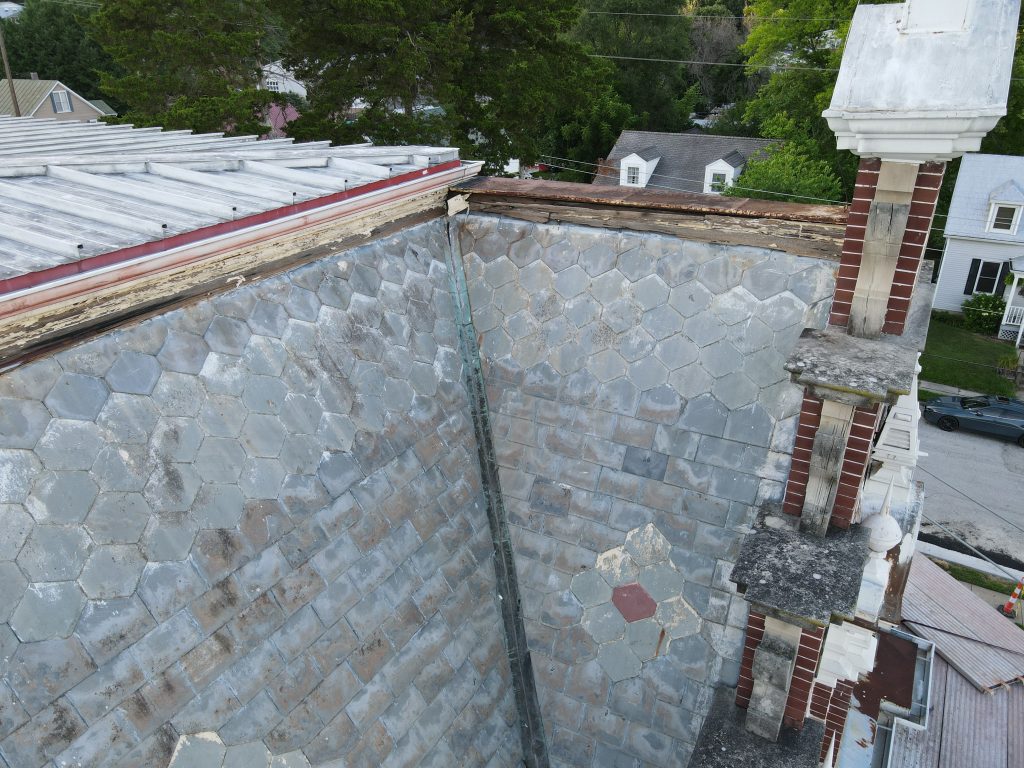
Upper Gutters
When the flat roof above the mansard was installed in the 1990s, a k-style gutter was hung and painted red. We are replacing the aluminum gutter with copper, which will sit right above the new crown. Custom copper scupper boxes are being fabricated with 3-inch downspouts leading to the inlaid gutter.
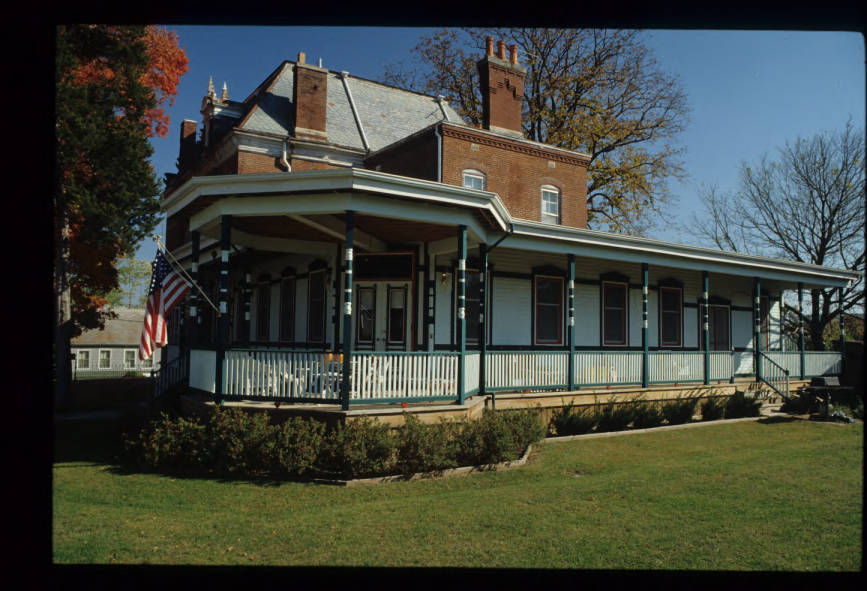
Skylight
The backside of the mansard features a skylight door. It is the only window for one of the third-floor bedrooms and acts as an emergency exit. We are replacing the skylight door with a custom-ordered replacement from Velux coming from Denmark.
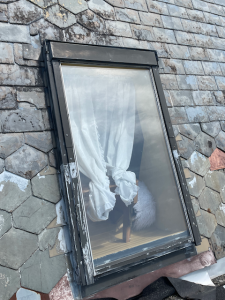
Radius Hip / Ridge
As mentioned, most of the metal is terne-coated steel. The radius hips and the ridge behind the front parapet will be replaced with copper.
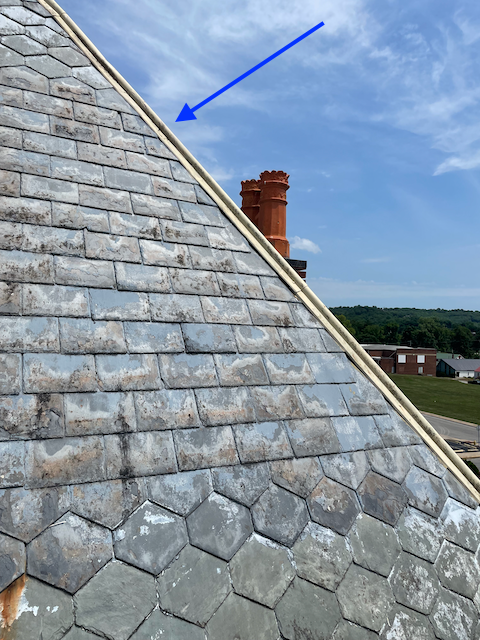
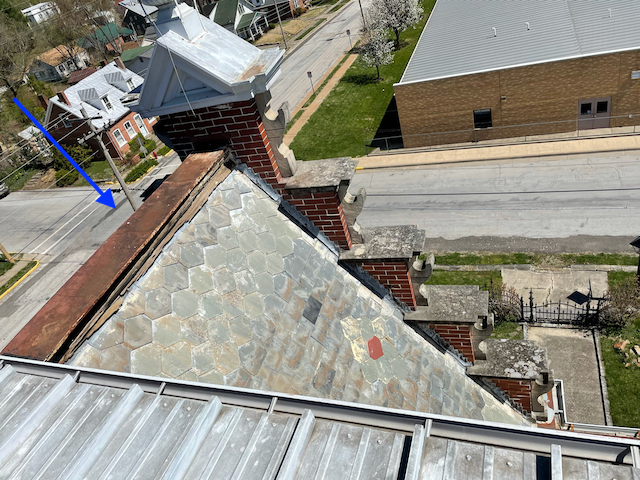
Soffit & Fascia
The south-facing side of the house needs the most work. The number one issue was when the gutter system was hung in the 1990s; it was not continued all the way around. As a result, water has been running over the fascia and brick for decades. We are going to solve this problem by rebuilding the inlaid gutter. From there, we can replace the soffit and fascia. At a later point, we plan on repointing this side of the house.
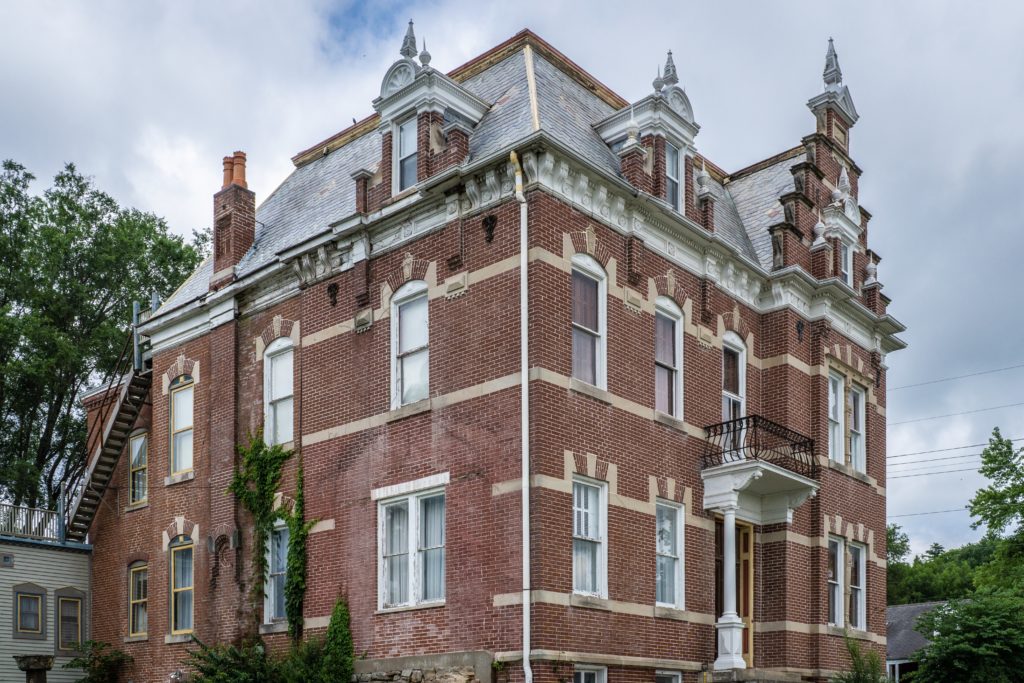
Timeline
Below is an overview of where we are at the time of writing.
- We finalized the construction plan in February. The goal was to start work in late spring.
- The Vermont slate is ordered in March.
- In late March, we learned there was a delay for the Vermont Black due to slowdowns at the quarry. Either we go with a Vermont Gray Black or wait an additional ten weeks for the Vermont Black. We chose to wait for the black, which closely matches what is original to the roof. Waiting for the black slate pushed the timeline from late spring into early summer.
- The slate arrived in St. Louis in May. We are waiting on the copper and for the team to free up from their current project.
- Scaffolding is erected the week of July 4th. First up is removing the existing roof, shoring up the decking for underlayment, and beginning work on the inlaid gutters.
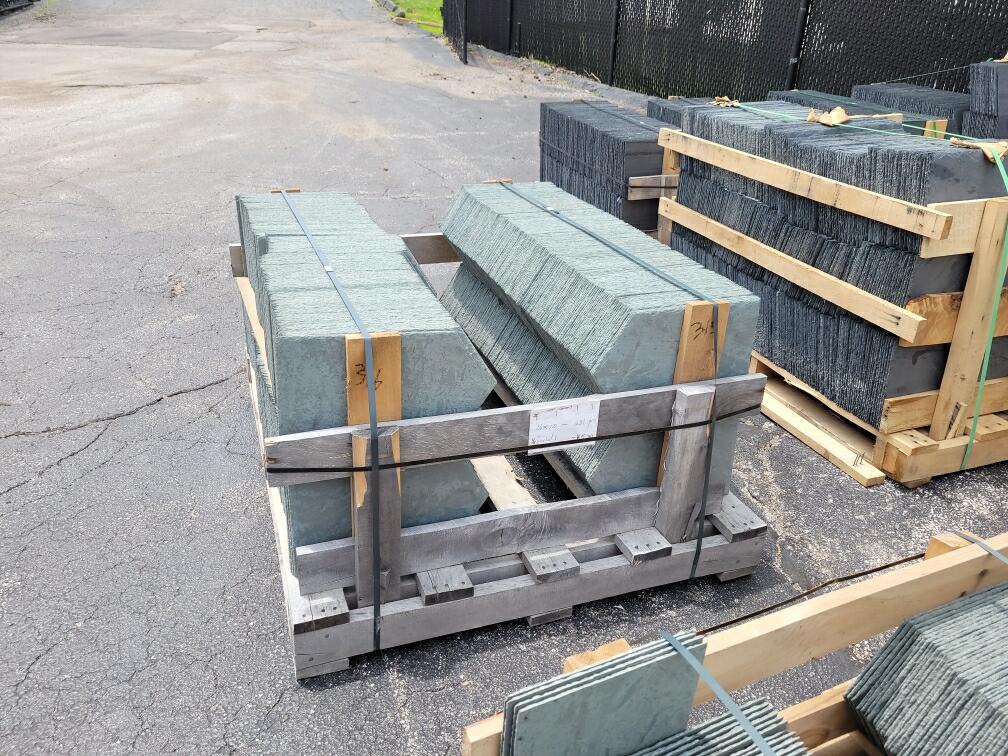
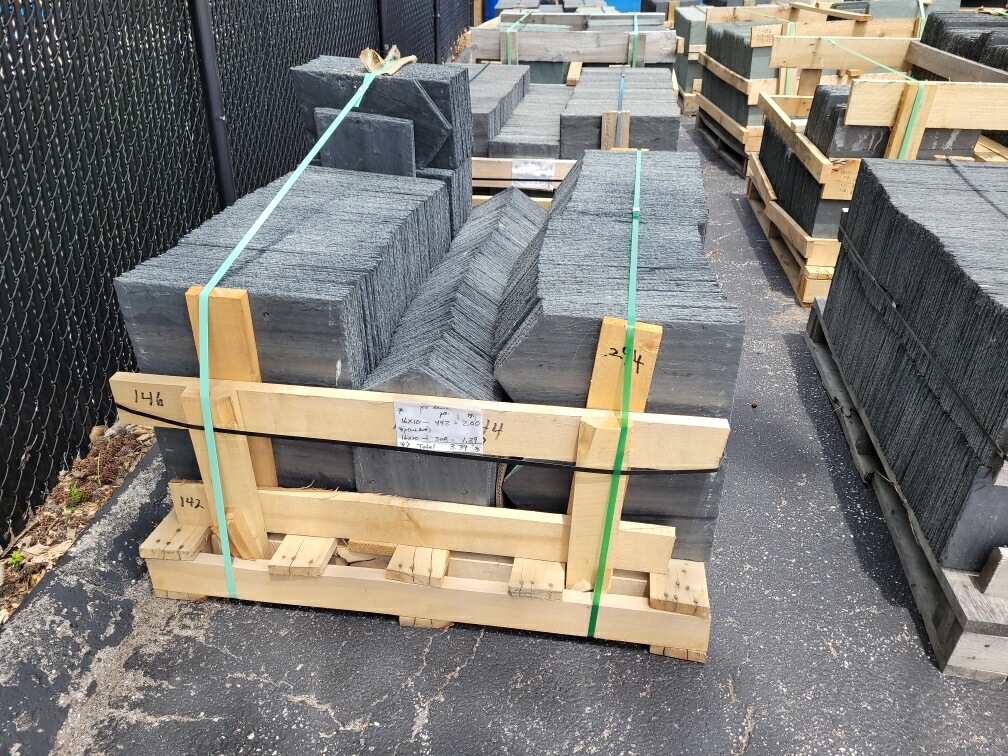
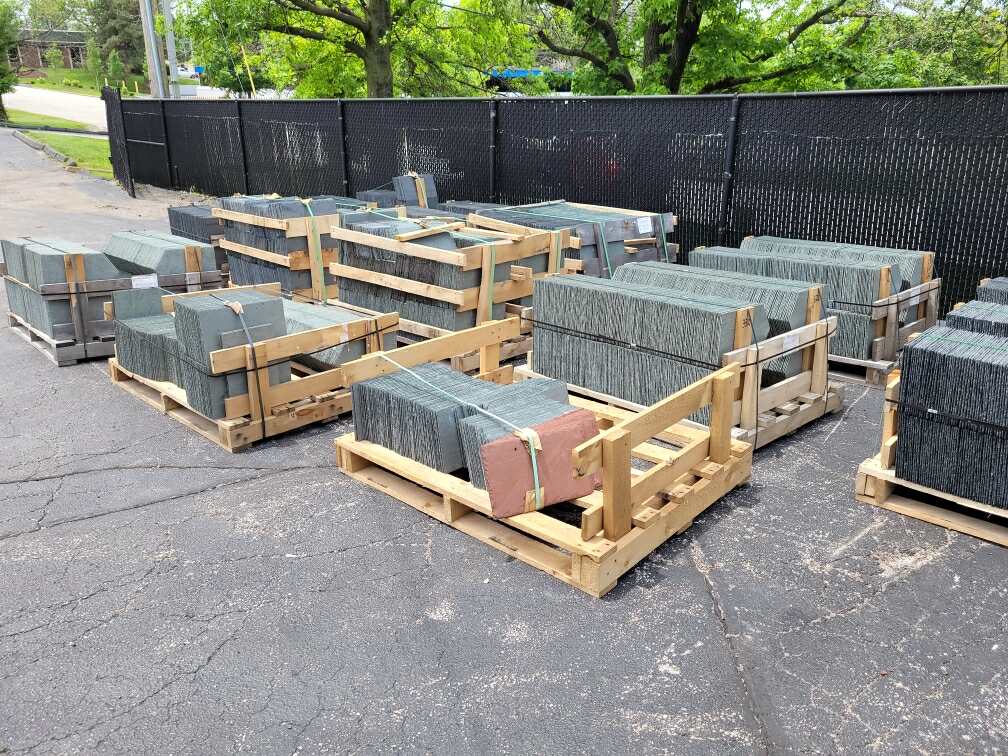
Thank you for reading, Michael and Alexandria Morgan
Continue reading Part 2: Architectural Built-in Gutters.
- The Slate Roof Bible by Joseph Jenkins, Third Edition, page 285 [↩]
2 replies on “Mansard Roof – Part 1: History & Planning”
Wonderful that you care enough to do it right! It will be beautiful!
Sounds like a job being done right. It’s better to do a job the right way so you don’t have to repeat it later. You have done your homework. Good job. Can’t wait to see the final outcome.
Love you guys.